In these harsh times where all certainties become uncertain, I’d like to emphasize the value of data-driven remote service.
In the old days, we were keen to check-in on our customer around the corner, drink a cup of coffee and help solve any problems. This was personal, friendly and pleasant but also time-consuming.
Over the past few decades, our society has increased focused on being productivity-driven, beating competition and enlarging business at a global level. This has expanded the customer reach that suppliers must serve, bringing logistical-, service- and timing-challenges: time is money.
Solving problems from a distance
Sometimes, stand stills are unavoidable because maintenance must be done, and problems occur.
But we all face the challenge to keep downtime as limited as possible. This requires planning, immediate action and quick response times.
You may also like to read the Preventive Maintenance series of blogs from my colleague John Beltman
Best scenario is if we can deeply dive into the machine to check and solve issues - from a distance.
All software-related issues can be easily taken care of this way, but in cases where parts must be replaced, or maintenance is required, needed are spares and maintenance products on the spot and people that are trained and equipped to take action.
With MPS flexo presses remote access is possible, thanks to modems that enable us to connect directly to the heart of the machines. Via our remote diagnostics and logs, we can see exactly how your press is performing, determine and resolve the issues, or determine next steps.
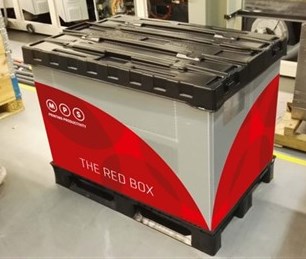
Our dedicated kits with crucial spares (Red Box), consumables and maintenance products make instant replacements possible and avoids unnecessary downtime.
Learn more about the Red Box by watching this video
And from our training programs, your operators and engineers are well-trained and can take the action needed.
We constantly monitor their skills and, when necessary, re-train to ensure they know how to service their MPS press. This way, together with operators and maintenance engineers, we’re able to check the status of the machine and define what must be done to operate the machine at its ultimate performance, or in case of a failure how to get it up-and-running again quickly.
Lifecycle Performance Program
Today, we’re also able to monitor the operation of the machine and detect unexpected and deviating actions that limit the maximum efficient operation of the machine.
Using algorithms, we can monitor if the machine is moving into production as quick as it should, if changeovers are done according to the norms and if speeds are maximized. This helps ensure production time, set-up and waste levels are reduced.
Based on an analysis of your jobs, we can calculate the most efficient way of producing and work together with you on possible improvements. We call it the MPS Lifecycle Performance Program.
Over the years, we keep your machine in optimal condition, your operators maximally motivated and trained, and we monitor the efficiency of operations together with you to analyze if productivity is at the max.
You’ll be amazed by the effects that tiny improvements have on your business results. And we’re happy to offer advice and help you reach the next level in your business development.
With the Lifecycle Performance Program, we can help significantly increase your productivity level, and show how it directly contributes to your profit level.
The advantage is that, especially now in times of crisis, this is all done remotely. We don’t just focus on the machine, but on your entire production process as an integral activity. We call it Beyond the Machine.
Would you like to know more about Beyond the Machine and the possibilities of remote service? Please don’t hesitate to send me a message.