When I’m speaking about the possibilities of development within MPS, I’m the perfect example myself. In 1999 I started working at MPS after my Intermediate Technical School (MTS in Dutch) as a bench worker. After working as a Mechanic in the Assembly for 6 years, I went to the Service department where I worked as a Field Service Engineer for 11 years. Because I wanted to spend more time with my family, I then went to the Commissioning department, where I became the manager in April of this year.
In this blog, I will tell you a little bit more about the path of development and educational chances within MPS as an organization, in the field of Assembly, Commissioning and Service.
Pre-assembly and end-assembly
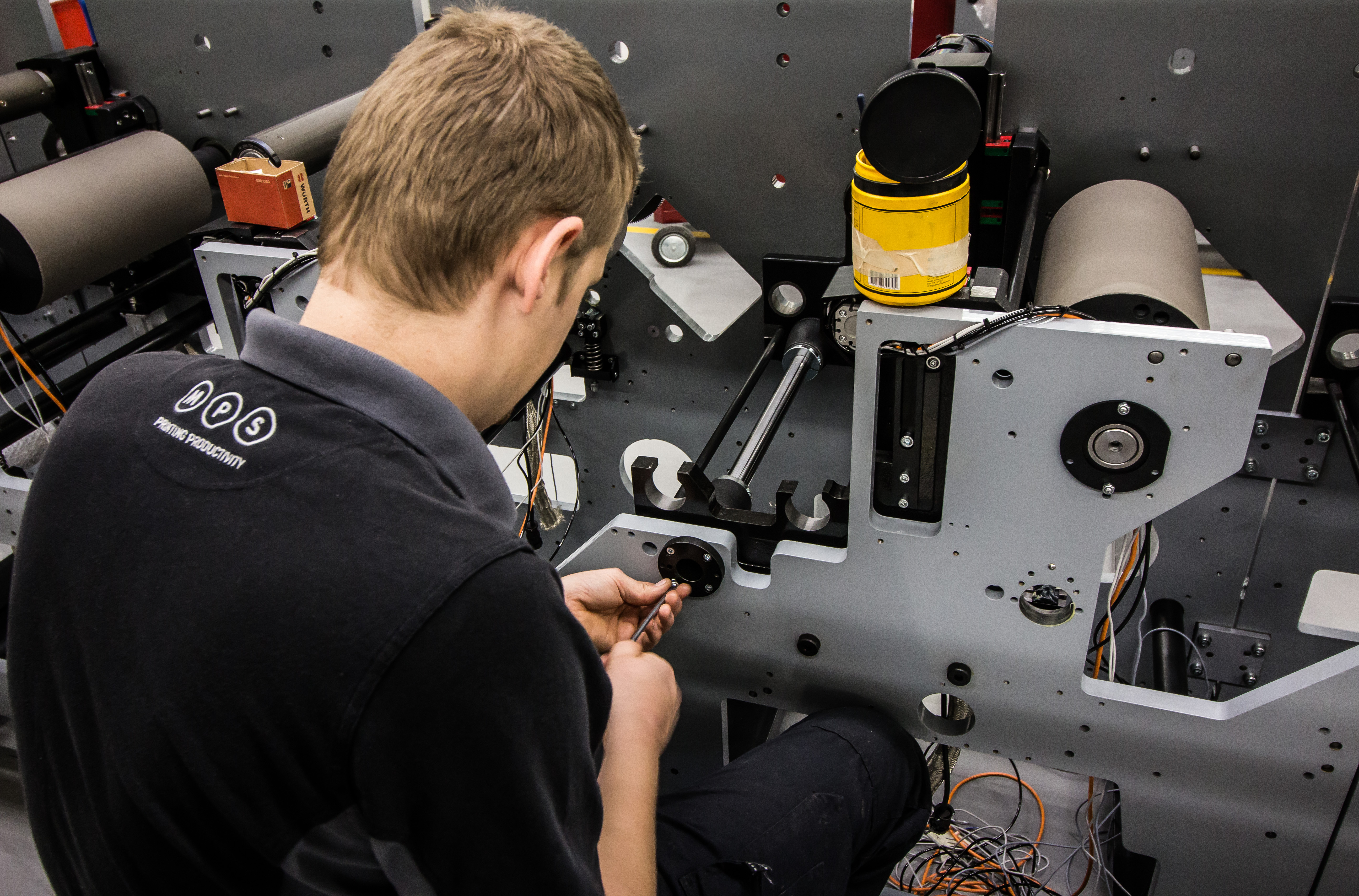
At MPS, we have an Assembly department that is divided between the pre-assembly and end-assembly. In the pre-assembly, the printing heads of different types of presses are mechanically built, just like all rail units, die-cutting units, etc. In the end-assembly, we start by setting up the frame of a new press, followed by the pre-assembled modules. The main drive, that consists of gearboxes, gear wheels and driving shafts, is then assembled. After completing this, we build in the UV installation and connect it electrically. When all the platework has been mounted on the backside of the press, we add the rail for the rail units. With this added, the assembly ends with a complete press!
Working at MPS as a (Junior) Mechanic
Within MPS, we have Mechanics from different educational levels. Most of our Mechanics started as a Junior after their Mechatronics studies in MBO (secondary vocational education) level 3 or 4. There are also guys (it’s a men’s world in here) starting after a dual route (combining studying and working) on level 2.
The tasks of a Junior Mechanic are: assembly and calibration of the modules that are to be built onto the frame of the press. With the assembly, technical drawings and parts lists are used. On these parts lists, all parts are specifically listed. The quality is maintained with the use of checklists. The Junior Mechanic also needs to have some knowledge of electrical schemes and connections.
From the Junior role, you can grow into the next step: Mechanic. The Mechanic, mostly working in the end assembly, is – next to the Junior tasks – responsible for the mechanical connection of carefully tolerated container guides, gearwheels and drive trains.
The next level in the development of a Mechanic, is the leading role. The Leader is responsible for the assembly of a complete press. He leads the Mechanics for the project and guards the process from A to Z.
The next step: commissioning
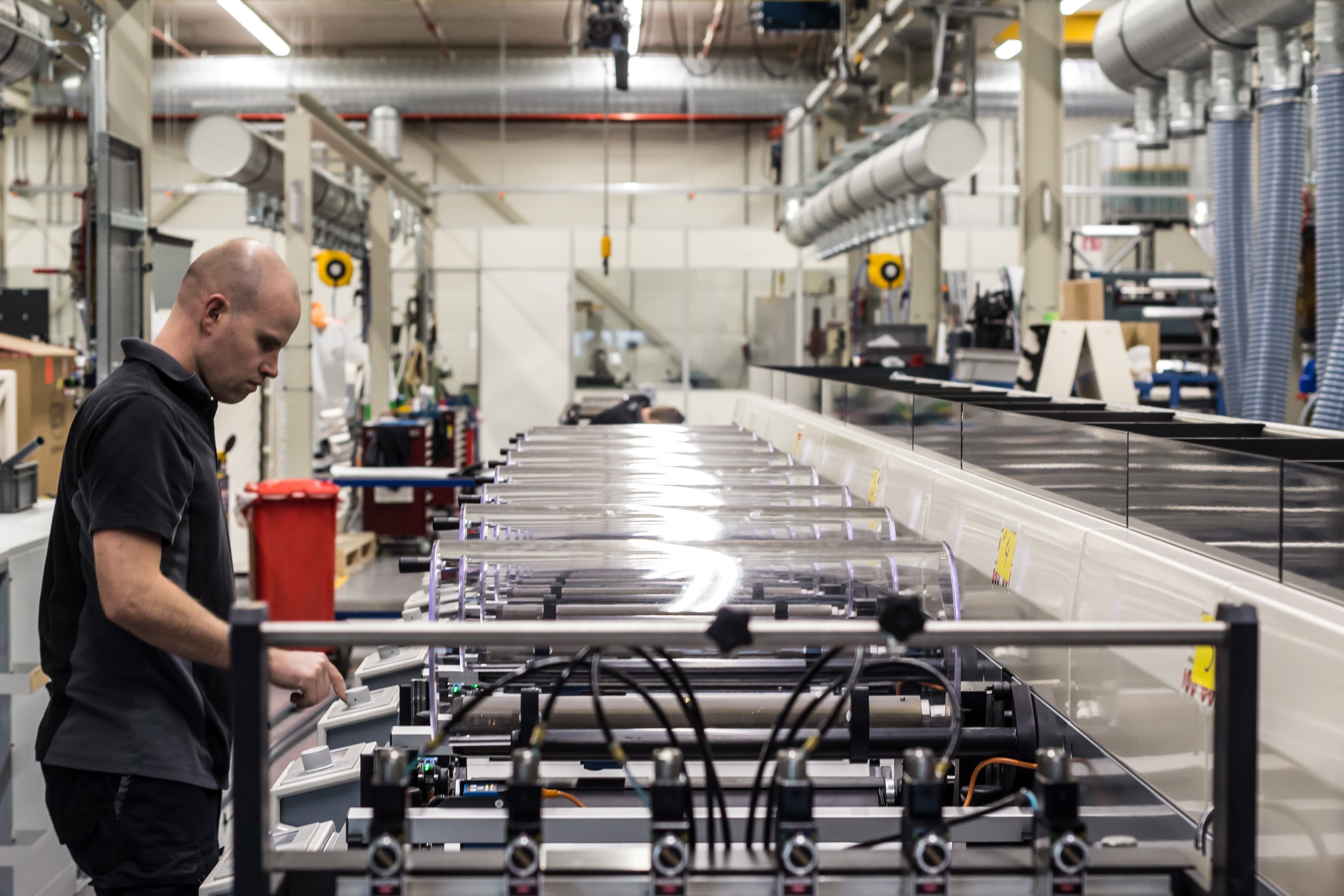
When a Mechanic has enough knowledge and experience as Leader, he can grow into the Commissioning department. As a Commissioning Engineer, you’re responsible for the delivery of a well-functioning printing press. When the press is complete mechanically and electrically, the commissioning engineer starts loading the software of the various electrical components. Think of MLC, servo drives, HMI and other control panels. When the software is loaded, the adjustment of the print heads starts, and the web tension is controlled. The Commissioning Engineer makes sure the press meets all the needs and expectations of the customer. When the press is tested following a protocol, the customer comes to the factory for the Factory Acceptance Test. During this test, as a Commissioning Engineer you’re the press operator showing all the functionalities of the machines. During an FAT, you’re in direct contact with the customer.
Field Service Engineer
When a new press is accepted by the customer, the machine will be de-assembled and packed, and the Commissioning Engineer watches the order completeness carefully. As a Commissioning Engineer, 25% of your time can be planned for Service support, meaning international travels for installations at customer sites worldwide.
Are you interested in the experiences of an MPS Field Service Engineer? Read this blog from my colleague Thimo Laan!
For those fond of travelling, it’s possible to make the next step and become a Field Service Engineer. The travelling frequency is much higher here; up to 70%! I can definitely recommend this if you’re looking for a diverse job with a lot of travels.
MPS Academy
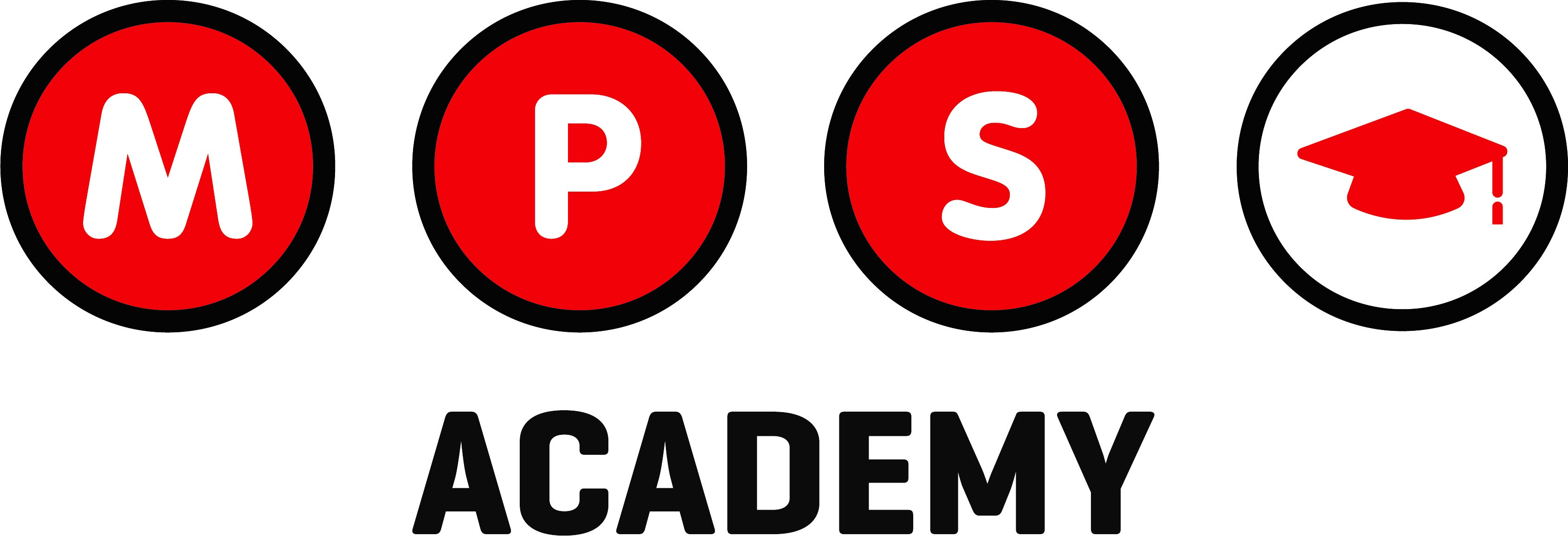
Within MPS, we think it’s very important to enhance the knowledge of our employees for his/her current, or future role. Wishes for training or courses are therefore always taken seriously, and usually accepted. We have also founded the MPS Academy for internal and external training. My colleague Leopold der Nederlanden gives various trainings about printing technology and the way our presses work.
I like seeing how everyone at MPS is very driven and committed. We make a great product together, which is something to be proud of!
Would you like to know more about working at MPS? Check this page, or contact us!