In addition to an eye-catching design, the type of substrate used to print a label or flexible packaging also plays an important role.
There are many types of substrates for printing and converting requirements: from different types of poly to self-adhesive, paper, foils, nylon, cellophane and more.
In this snippet, I’ll go through the three most popular substrates used in labels and packaging. I’ll also cover an important issue that is sometimes overlooked: the use of sustainable substrates and recycling.
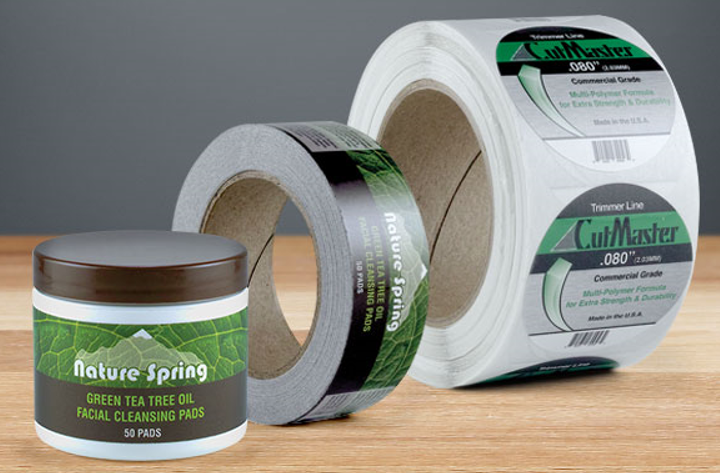
Self-Adhesive
Top of the list as most popular for labels are self-adhesive substrates. Ease of application and printability are among the main reasons.
Self-adhesive labels are used in products from wine and spirits, health care, cosmetics, food packaging and more. Self-adhesive substrates are common in peel and seal or permanent label applications and come in many types, such as metalized, paper, white and clear films with different finishes from matt to gloss and film glassine or paper (backing or release substrate).
The ability to de-laminate and re-laminate makes it possible to create double-sided labels or apply a glue deadener for tabs, multi-layer labels and more.
Learn more about the advantages of multi-layer label printing
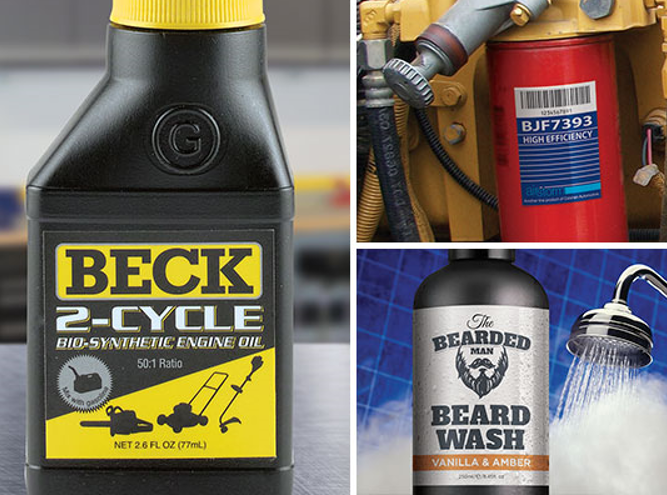
Poly-Based Substrates
The packaging industry is a large part of the print industry – packaging is all around us everywhere we go. Among the most common substrate are poly-based materials due to their inherent strength and flexibility.
Poly-based substrates can be harder to run due to their stretch. Consequently, heat, chill drum temperature and tension are especially important in ensuring the correct repeat length is achieved.
Typically, poly-based products run on wider web presses but are also used for narrow web applications. The EXL-Packaging is our specialized packaging press; but these substrates can also run on the EF range including the EF SYMJET hybrid flexo inkjet solution.
Aluminium
Aluminium comes in various types, from thin foil for confectionary to thicker types for pharmaceutical tablet (blister) packs and even thicker for cans and lids etc.
The process of making foil is very interesting; the foil starts as aluminium ingots that are heated and hot rolled into a thin roll. The roll is then split and rolled further, multiple times, until the required thickness is achieved. This can be as thin as 0.006mm or 6um.
Tip: There can be many issues that arise when printing with foil. If it is thin, like the foil used for wraps, it can be useful to put a web through and join your foil to the poly. Before make-ready remove the poly. Also, watch for rollers with dents as any imperfections will show up very visibly in the product.
Paper
Paper come in many different types and for many different uses, from Newspapers, Stationary, Magazines and many others.
In the Narrow Web side of the Print Industry, we typically use paper ranging from 27gsm to 330gsm. This can be less or more.
Priming substrates
Before printing, it can be necessary to prime certain substrates such as porous substrates, polypropylene, polyethylene, and others.
In flexographic, offset, screen, and digital printing, priming helps the ink to key or bond to the stock. Priming can also be done in spot areas where the screen printing is having problems, providing a pre-lay-down to allow the ink to achieve a satisfactory lay-down.
For gravure you can use a spot varnish under special silver inks to give it a shiny, silver foil look for a simulated foil. Transparent colours can be added over the silver to give your simulated foil the colour required.
Corona treating
For corona treatment of the substrate, it’s very important to maintain the correct surface tension of the substrate as this will help the ink to adhere (the term commonly used for this is keying).
Dyne pens are the easiest way to check your corona level on your substrate. Between 32 to 44 is in the most effective range for most inks. Poly can, however, be less (see the chart below for reference).
If the corona is too high, this can result in poor adhesion of the ink to the substrate, so often it’s the case that more is not better. When using a dyne pen, if the line breaks into droplets then it’s not suitable for printing pens in the range from 28 to 56.
Testing is the key to finding out what’s best for your requirements.
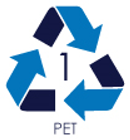
Don’t forget: Recycling
Choices to recycle substrates are increasing every year, giving the print industry more options for using recyclable substrates.
The use of wood-based plastics instead of fossil-based plastics helps to reduce the carbon footprint of your company and your country. Government of most countries offer companies incentives for reducing their carbon footprint. The use of recycled substrates also helps with the growing landfill issue.
Our industry is increasing in size every year and now is a great time to start recycling, especially during these last 6 months in which, because of the COVID-19 measures, production has significantly dropped.
I hope this has been helpful. If you have any questions or suggestions you can always contact me via LinkedIn or via email k.marsh@mps4u.com.