If you’re in the printing industry, you know there are thousands of variables that can affect the machine running smoothly and ultimately the print quality.
In this snippet, I’ll go through one issue that can affect the smooth operation of a printing press and some possible causes and fixes: web breaks.
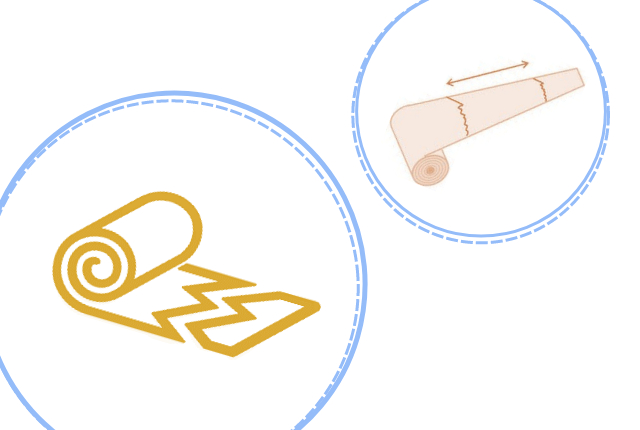
Causes of web breaks
A web break is a frustrating issue printers face. There are many reasons why they occur, and multiple ways to help prevent and fix them.
When it happens, how big the wrap around is and how many units it passed through can affect the time and complexity of getting the machine back up and running again.
Roll changes happen multiple times during a shift. If some simple things are missed, it can result in a web break at every roll change. Inspection, care, and full attention must be observed.
Other problems can arise during a roll change, job change, and general press setup. One or a combination of these issues can result in your press not operating efficiently and resulting in web breaks.
Here are a few of many issues that cause web breaks, why they happen, and how they can be fixed:
Issues:
1. Nicks and cuts at the start or in the sides of roll. Damage can be caused by shipping, warehouse storage, or even when loading rolls on the press.
2. Poor taping at the unwind splicing table. Can be caused by poor training, lack of attention, or using poor quality/wrong tape.
3. Incorrect web path. If the press is webbed up incorrectly this can cause web breaks from missing rollers or even running the web the wrong way.
4. Tension settings. The nip roller infeed or outfeed is not on or set at the proper pressure setting; too low or high tension is set for the type of substrate; or the unwind shaft is not inflated.
5. Accidents. Dropping rags or tools on the web will cause web breaks, as well as an untrained operator removing labels from the unwind roll.
Fixes:
1. Contact the Print Supervisor to report the matter. Depending on the damage, they will determine if the roll can still be used and if follow up action is required. If damage is minimal, the operator can remove a small slice from the top of the roll. If the damage is larger, cutting the roll back may be required - and depending on side damage the roll may need to be rejected.
2. Proper training for splicing, attention to all roll changes especially between different substrates and watching for poor quality/correct tape.
3. Always know your web path. If you’re unfamiliar with the web path, refer to another press. If this isn’t possible, refer to a web diagram for the different sections from unwind, printing stations, embellishments, die and rewind. If you miss things such as load cells for tension, this can also cause the web to be moved or get caught causing a web break.
4. Be in the habit of turning off the nip at the end of shift and turning it on at the start of a new shift. If shutting down the machine, record (if required) the tension setting for different substrates and ensure your unwind shaft is properly inflated. If your roll moves, depending on the length of your press, the web may break before you see the print vanishing off the paper.
5. It’s common knowledge that we shouldn’t clean or work on things while the press is running, as rags or tools can not only cause web breaks but personal injury as well, which can be very serious. If you are the printer, allow no one to remove labels off the web as it’s sure to end with a web break. It sounds simple, but this should be taken seriously.
There are many more issues causing web breaks such as rotation of the die unit, and presses that can run in both a forward and reverse direction. This can be caused by the operator not realizing the direction of the web: the wrong web up will cause a web break.
Having the correct web path knowledge and skills to determine why or how the web break happened is important in getting the press going again ASAP without short cuts. If new to a press, always double check or ask someone else to make sure.
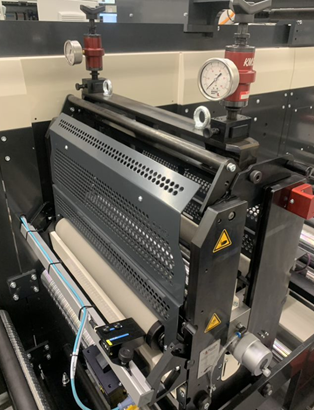
Importance of web break detectors
Correct placement of web break detectors is key. A web break detector is a sensor that with a light beam picks up the signal when paper is not there. It’s ideal to have them on the unwind, between all print units, die station, and rewind.
You can also set web break detectors to your minimum web width. If you set them too wide, when you go to a small stock the web break sensor will not detect the web, so you will need to adjust.
To check if they are working, cut a slice out of the web and make sure it stops on each sensor. If the sensor does not work it can be very costly in damaging plates, foil plate, embossing die, punch bars or your die and potentially put an end to running that job.
Wrap around
It’s especially important to be cautious when removing paper from a web break that resulted in a wrap around, especially if it’s a large one.
Take care in removing the substrate without damaging your steel path roller, nip roller, die or anything else it is wrapped around. If you score a roller it will be damaged and can cause marking on your web.
If it’s your die or foil plate etc. it can damage it and render it useless, expensive to replace, and could cause the job to be redone. If your print plate is damaged by the paper, then this is unavoidable.
UV lamp care
Sometimes paper gets caught in the UV lamps. If you think this is a possibility, it’s recommended to shut off your lamp and check for any paper inside.
If there was any substrate in there, you may just need to clean the reflector and lamp. If the damage to the lamp or reflector is too severe, you’ll need to change the affected part before running the press to prevent any printing issues.
MPS press x2 GEW UV lamps no web
Possible maintenance
It’s possible you’ll need to remove guards or parts of the machine to access the web break.
If the web break has bent guards, finger bars or any other issues, then maintenance may be required. This can range from straightening up the finger bar to replacing a bearing in the path roller, fix a broken belt or other problems.
Always make sure the press is 100% fixed and ready to go before continue running your print job.
Get in touch
The above is based on my experience as a printer. I hope this was helpful and gives you insight into some causes of web breaks and how to resolve them. The optimum defence against web breaks is the operator being aware and listening to their press.
I would appreciate any feedback or suggestions on this or any of my other snippets.
You can reach me via LinkedIn or via email k.marsh@mps4u.com.