In 1890, the first flexographic printing press was patented by Bibby, Baron and Sons out of Liverpool England.
Around 1990 is when big advancements in flexography began, as more companies started shifting to this printing process for flexibility and access to a wider variety of jobs and customers.
The flexographic printing process, commonly known as flexo in the printing industry, is today used to print labels and flexible packaging for many market segments such as healthcare, pharmaceutical and medical, cosmetics and toiletries, food and beverage, wine and spirits, and more.
Flexo’s versatility and its capability of running on many different types of substrates is one reason why flexo is a popular choice for printing companies.
How the flexo process works
Flexo printing is a rotary process utilizing a flexible polymer plate with a relief image. Ink is supplied by an anilox which consists of engraved cells on a ceramic coated roller. It’s like letterpress but is a flexible plate versus a flat metal type held in a chase base.
The anilox cell is like a bucket which holds ink and is measured in lines per inch, usually ranging from 80 to 1200 LPI (number of cells in one square inch of the anilox surface). The depth of the cell is measured in billion cubic microns (BCM) equating to the volume of ink each anilox cell holds.
These two measurements combined provide a controlled method for selecting the right anilox for the type of image you will be printing. This gives the printer flexibility to choose the correct anilox e.g., 700 LPI x 4.0 BCM for a plate which has a screen or process colour for pictures, etc.
The lower the LPI the more cells per inch - resulting in a larger cell providing more ink to the substrate. With BCM, the ink cell depth will determine how much ink the cell will release to the substrate, which is why anilox rolls must be thoroughly cleaned.
The flexographic print unit consist of an ink tray/pan, pan/fountain roller, anilox, chamber or doctor blade, and your printing plate.
Chamber blade
A chamber blade set up has a chamber with two blades that are against the anilox. Excess ink is wiped off the anilox before transferring the required amount of ink to the printing plate, then to the substrate which runs over an impression roller.
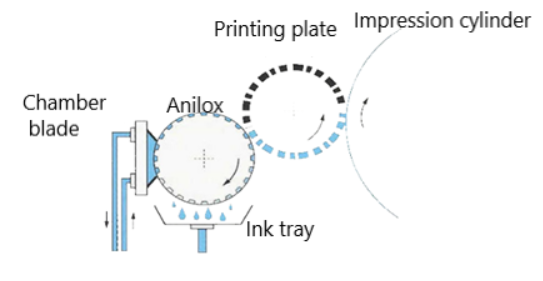
Doctor blade
For a doctor blade set up, ink from the ink tray will transfer from the rubber roll to the anilox. A single blade wipes off excess ink leaving the desired amount of ink on the anilox to be transferred to the plate. The substrate then passes over an impression cylinder.
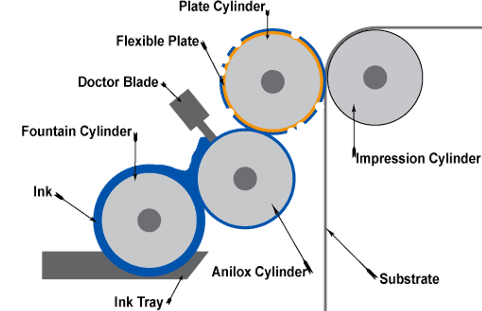
Raising the bar in print quality
Flexo plate technology has higher lines per inch (LPI) or lines per centimeter (L/cm), and when used with HD plates it provides amazing print quality with very fine details.
This is also possible with technology in the anilox rollers used to transfer the ink to the printing plate. With recent developments in flexo plate and anilox roller technology, print quality is comparable to offset printing - including microtext printing.
Advancements are also in the printing press such as servo-driven machines that are constantly improving. Inking systems, blade holders and doctor blades also allow for more precise ink control to the anilox. Free rotating impression rollers help reduce drag with the plate acting as a nip roller.
Print sleeve technology is also improving with a more true, lighter, and durable design to help provide consistent print. Registration systems can provide lateral or length register. Finally, increased press speeds are raising productivity while maintaining high quality print.
MPS flexographic printing press unit
Flexo advantages:
- Quick changeover times
- Easy set up of printing unit
- Versatility
- Multiple ink selection: water based, UV inks, solvent inks and dyes
- Wide range of substrates
- Automation
- Options to add other types of printing
- Embellishments: die cutting, embossing, hot and cold foil
- Lamination: solvent, solventless and water-based (also in register lamination)
- De-lam and re-lam
- Multi-layer labels
- Dual web
- No VOC emissions of UV and water based flexo inks
Print units
With flexo printing, printers can also add other printing processes to their press with additional units either inline or on a rail system, such as:
- Rotary screen printing for high build varnish and crisp white type, etc.
- Gravure for simulated foil, opaque white back grounds, primers and more
- Offset offering high print quality for pictures. (Note, offset is not available in rail units due to the size of the unit and requirement of water to clean the non-image area of the plate in the printing process)
Rotary screen printing on a rail system
Final word on flexo
Cleary, flexographic printing has a lot to offer the printing industry.
With its simplicity, efficiency, low running cost, many uses for all types of jobs, and versatility of applications to complement the final product being printed, flexo printing is taking a large hold of the market.
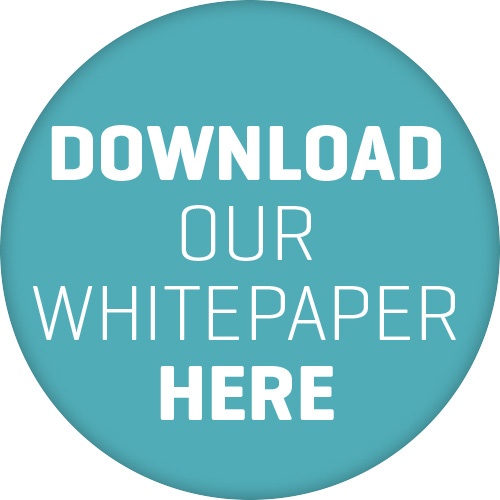
Current technology and advancements in plates, inks, aniloxes and substrates makes the choice of flexo more popular for print companies looking for increased product diversity.
Get in touch
This is just a brief snippet on flexographic printing. I would appreciate any feedback or suggestions on this or any of my other snippets.
You can reach me via LinkedIn or via email k.marsh@mps4u.com.