The ultimate goal of your flexo press is a printed roll of high quality labels that will keep your customers coming back for more.
So, why is line count so important? Well, if you want to print a detailed image, a high line count is what you need. However, it is much more difficult to print with a high line count.
That’s why choosing the right line count for your flexographic printing plates is essential to get the desired output you need. In this blog, I will explain when to use which line count (high vs. low) and share some best practices with you.
https://www.youtube.com/embed/mefY0kIXryo?start=114 factors that determine which line count to use
In general, there are four factors that help you choose the ideal line count for your flexographic printing plates:
- The viewing distance
- The required degree of detail
- Available anilox rolls
- The precision of the printing press (register and print tolerances)
If you have this information at your disposal, you can determine which anilox line count is best.
Line count & flexographic printing plates: best practices
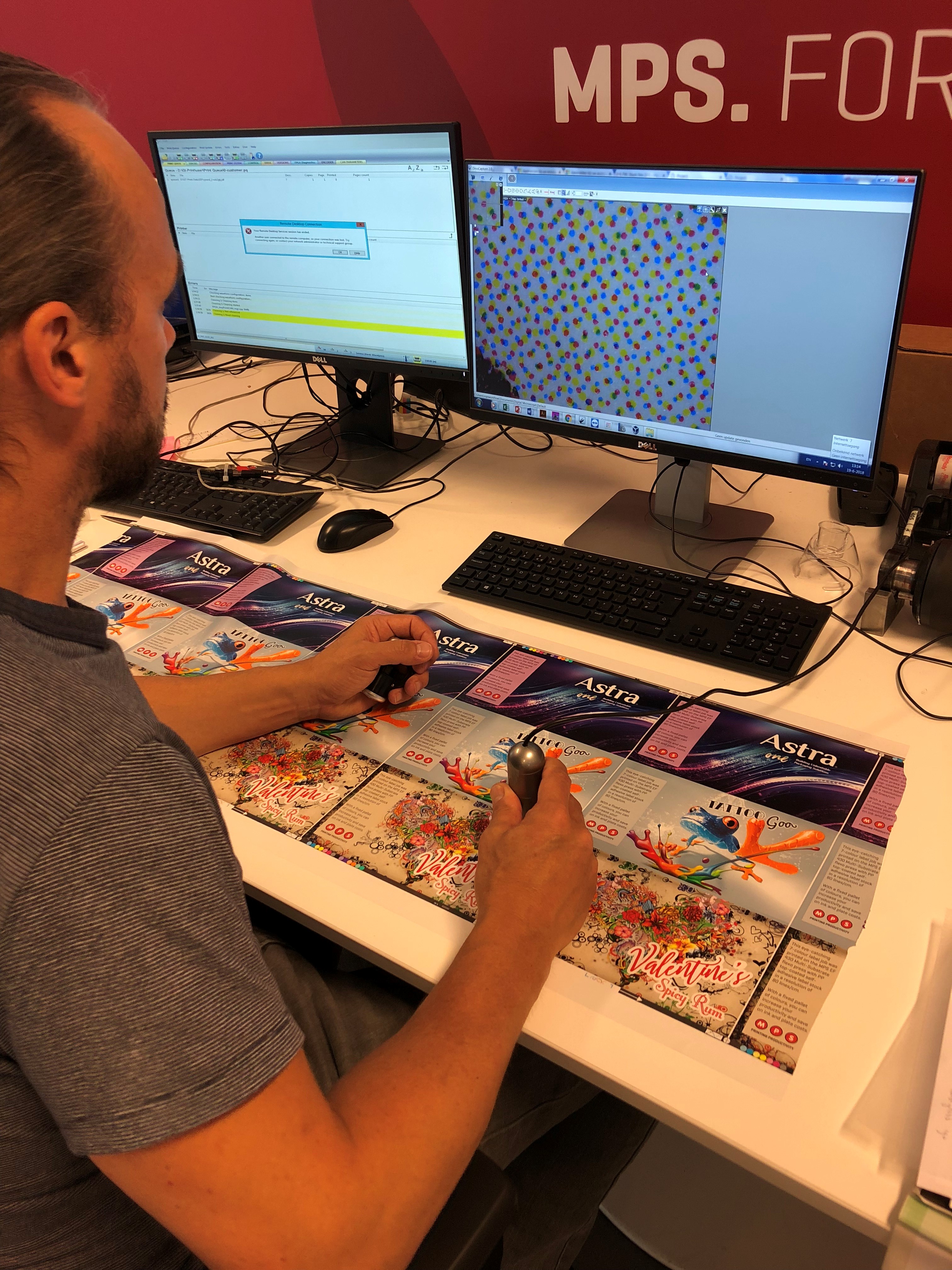
Now, taking a step further in determining which line count to use — and what you additionally need to get the desired output — I have listed some best practices to consider for both high and low line count.
High line count
With high line count, in a short distance you can see fine details or structures within a picture. High line count produces very bright and colorful labels to attract attention.
However, just a high line count isn’t enough to print in the quality you need to meet your customers’ demand. You also need a printing press with a very small register tolerance. Why? Colors that aren’t exactly printed on each other will cause blurring, and the detail you are after will be lost.
When using a high line count, it is also important to print an ink layer as thin as possible. This thin layer ensures that the high line count in the printing plate also remain as small dots on the printed output. However, the color of a thin ink layer is less vibrant compared to thick ink printing. This difference in color means you need highly concentrated printing inks, like UV inks, to meet achieve equivalent vibrant color requirements.
In short, to print with a high line count, you need:
- A printing press with a very tight register tolerance because small deviations have a big influence on print quality output
- A thin ink layer to ensure the desired quality
- Highly concentrated printing inks (UV inks) to meet color requirements.
Low line count
If you want to print a label with ink variation — for example dark to light or light to dark — it is difficult to do this with a high line count. It becomes easier with a low line count. Why? Because the printed dots aren’t as close as with a high line count and the spacing between them is less likely to fill up with ink.
In general, it’s easier to print with a low line count as the printed dots aren’t as close as with a high line count. Because of this, the printing plates will not be filled in with ink.
However, due to the advancements of inks, anilox rolls with finer structures and better ink delivery, along with high-definition printing plates, finer details can also be achieved with low line count. Technology developments with flexographic plate imaging in combination with press capabilities have also opened the door to a new method of producing security and 3D motion flexo roll labels.
We’re here to help
At MPS, we are well aware of the additional factors you need to print with the right line count to get output that meets your customers’ requirements. We know you need a printing press that enables exceptional precision to deliver output with unprecedented detail.
If you have any additional questions about line count in general or wish to further discuss which line count is best for your application, our specialists are here to help.