Based on our philosophy of ‘Share Expertise, Multiply Benefits’, we heavily invest in various training programs to guarantee skilled personnel and a high level of service.
To facilitate this, the MPS Academy was established as an internal program where staff can receive ongoing training and participate in workshops and courses to advance within the company.
Intensive introduction program
First of all, we make sure that every new MPS colleague becomes quickly familiar with the organization and our processes. Our HR Advisor Martine van der Meijde set up an introduction program, where new employees participate in meetings and trainings throughout all the departments at MPS. Depending on their function, they will accompany some of their colleagues to see what their work day looks like and a first-hand impression of the processes involved.
New colleagues learn all about MPS machines and processes
Internal sessions
MPS invests in 40 hours per week for trainings - for customers, agents and employees.
For example, MPS engineers and service experts receive training sessions on material, UV inks, localising problems and more. My colleague Leopold der Nederlanden (MPS Print Manager) set up a program where he teaches about colour management, our machines, the different printing techniques and a flexo printing special. Theses sessions are not only theoretical, but we practice what we learn directly on the machines in our Technology & Expertise Centre.
Training sessions are provided by our own experienced staff or by our suppliers.
Quality management
Quality management is also very important at MPS.
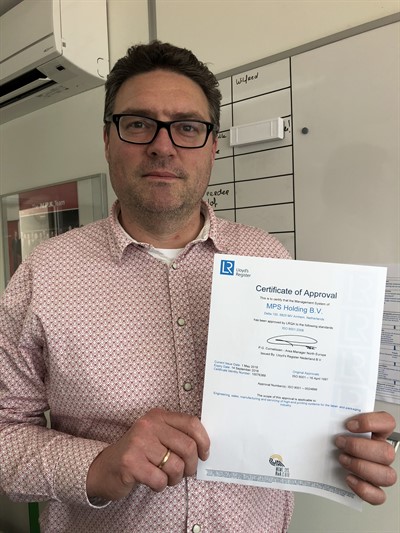
A system is in place to track which modules employees have successfully completed, the certificates they have and their competences and experience. So, if we have a call from a customer, we will know exactly who has the needed knowledge.
We regularly conduct internal audits to ensure our processes are being strictly followed, and our employees are trained and competent in conforming to the quality requirements in place.
MPS recently received a certificate of approval for the ISO 9001:2008, which means our quality meets strict requirements and have high-qualified technical personnel that oversee the entire production process.
Keeping updated
It’s important for everyone to keep learning and be continually updated on developments in the market. We often have external training programs or seminars such as electro mechanics, software, hardware solutions, engineering trainings, print management, and more.
Several of my colleagues recently attended a course on lean manufacturing, to learn more about reviewing and improving processes, procedures and the workplace, and are now Lean Six Sigma Certified. Several engineers attended an electro training one evening every week for seven months, and are also now certified!
MPS also ensures its agents are well trained and informed, and know everything about our products. We make sure they understand how we build our machines and how to recommend the right machine configuration for our customers.
We also attend several international congresses, tradeshows and industry association meetings. Make sure you meet us at one of these upcoming events!
Operator training
Our machines are Operator Focused and our team is highly qualified. It’s also important that the operator responsible to run your press is well-trained too, as John Beltman, MPS Project Manager explained in his blog: Why operator training is key.
We’re busy improving our operator training program, to create a program built on modules. Based on the experience of the operator, we can recommend the right modules for a tailored training that meets the operator’s needs. Stay tuned for developments of this exciting new training program!
Interested in operator training? Contact us to talk about the possibilities and make an appointment.
Leopold teaches operators all about machine configurations,
The training is part of a GOC qualifying flexo training in the Netherlands
Learning opportunities for YOU!
We’ve recently launched some new programs such as FAQ Friday where each Friday we share a new video of an MPS Service representative providing a short answer (about 1 minute) to a common question received by the service department.
Also launched was a series of four webinars, where I explain how to set up a future proof printing process.
What’s next on the agenda? How-to videos! Subscribe to the MPS YouTube channel to be notified of these ongoing learning opportunities!